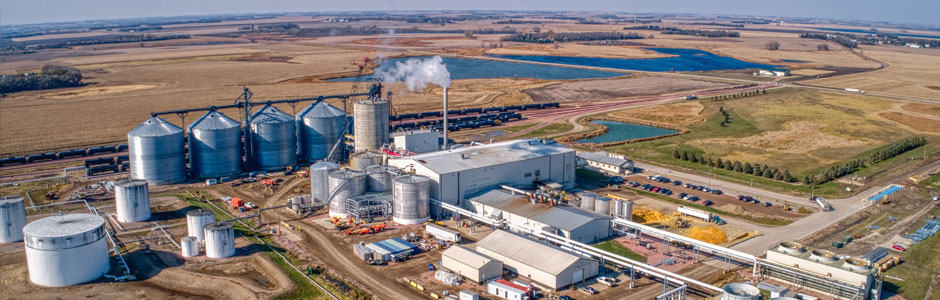
I. Challenges
A Midwest ethanol manufacturing plant replaced the membranes of their large reverse osmosis (RO) system but the differential pressures increased rapidly and exceeded the recommended operating ranges. If failure occurs, they will lose $200,000 in revenues per non-operational day. To cope with the problem, the ethanol plant carried out a Clean-In-Place (CIP) procedure but it did not restore the unit’s original performance.
II. Approach
Garratt-Callahan (G-C) water treatment professionals began to check the system. The in-house lab team tested the site’s private well water and customized a specific membrane autopsy. According to the test results:
- There was a consistent supply of iron-reducing bacteria that were not effectively removed by subsequent chlorination.
- There was a bacterial growth forming on the membranes.
A new RO performance monitoring system was implemented to give operators early notice of trends in pressure, flow and other critical parameters. This allowed the CIP procedures to be consistently scheduled before any damage could be done to the membranes and before the output quantity or quality could affect the plant’s production.
The new monitoring system included the following:
- A 30-minute circulation of chlorine dioxide solution was added to the routine CIP procedure
- A longer, non-oxidizing biocide soak was implemented during the bi-annual plant shutdowns
III. Results
G-C’s expertise completely restored the ethanol plant’s RO system’s original performance:
- The new performance monitoring system allowed plant operators to schedule the CIP based on more accurate warning signs
- The new cleaning procedures doubled the length of time between CIPs and maximized the lifespan of the membranes.
"*" indicates required fields