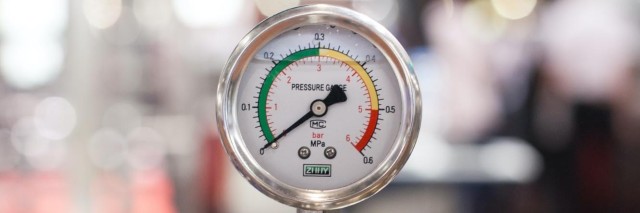
Maintaining Peak Efficiency and Avoiding Unnecessary Downtime
Industrial boilers are a necessary part of many establishments and can be found anywhere hot water or steam is required. Most facilities, from the ones that produce food to hospitals, require uninterrupted use of boilers every day.
Proper treatment is important for maintaining maximum steam production and avoiding unnecessary offline time. It is well known that boiler water creates deposits on the interior surface of the machine. Deposits may vary from scale due to concentrated minerals to those created by corrosion products. This leads to problems ranging from loss of efficiency to condemning an industrial boiler, especially in the low to medium pressure boilers.
How deposits form during 24/7 operation
Industrial boilers are run using water, often potable city water, that contains naturally occurring minerals – also called scaling species. The percentage of mineral content may be high or low depending on the water supply source. The deposit-forming potential is generally higher when the source water contains high concentrations of scaling-forming species. It is common to remove these types of offenders from the source water, but poor maintenance of feedwater softeners and unforeseen upsets often let them through. Alternatively, mineral contamination of condensed steam (recycled to the boiler) and corrosion products from various locations in the system will drive scaling and deposition.
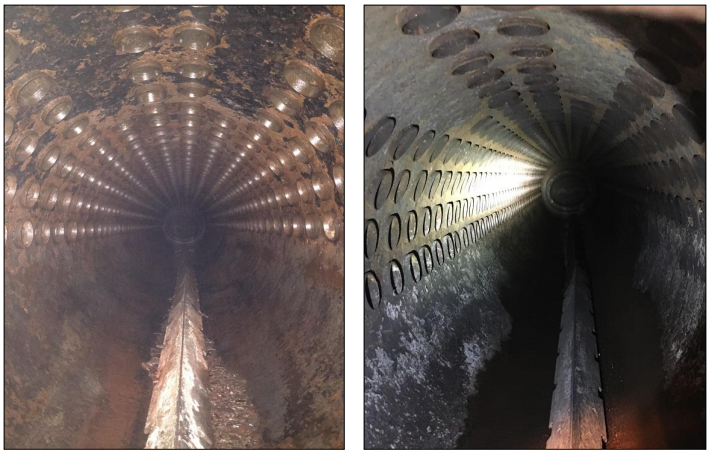
As water in the industrial boiler evaporates, minerals become more concentrated in the remaining boiler water. As the concentration of minerals reaches a saturation point, they start to come out of solution and deposit onto the internal surfaces of the boiler, presenting thermal stress.
The main species responsible for deposition are calcium carbonate and iron oxides (CaCO3, Fe2O3). Deposits form first on the boiler heat transfer surfaces, where temperatures are highest – reducing the transfer of energy between fuel and boiler water.
As a result, mineral deposits affect the efficiency of boilers and increase fuel waste by reducing the amount of heat transfer. The presence of scale during an inspection can result in unplanned maintenance for cleaning. If scale is difficult to remove and/or accumulates across multiple inspections, a facility may be faced with the consequence of condemning their boiler because it is unsafe to operate.

Controlling mineral deposits to maintain a consistent “clean-state”
Boilers that are treated properly can operate 24/7 without the need for routine cleaning, whereas boilers that experience long periods of neglect will almost certainly require acid cleanings. Acid cleaning is a form of maintenance that requires offline time, manpower and involves hazardous materials.
To reduce the potential for offline cleaning and generally keep the boiler interior clean, feedwater treatment, boiler water treatment, monitoring and testing can give way to a predictive maintenance cycle. The presence of minerals like calcium, magnesium is measured in parts per million or ppm. If the feedwater calcium hardness >2.0 ppm and magnesium hardness >1.0 ppm, it is extremely likely that there will be formation of scale and sludge.
Treating feed-water to increase boiler efficiency with the Garratt-Callahan Formula 1100 and 1123
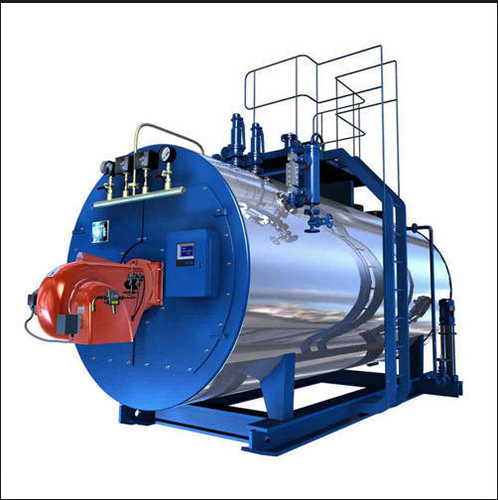
The Garratt-Callahan Formulas 1100 and 1123 contain highly active all-polymer scale inhibitors and sludge conditioning agents. These products, added directly to boilers or feed water, inhibit scale and work to remove deposits that have already formed. Formula 1100 cleans the boilers while online, preventing the formation of scales on the heated surface; the main risk factor.
Frequent questions often asked by our customers:
Q: Is my boiler a good candidate for treatment with Garratt-Callahan Formula 1100 or 1123?
A: Formulas 1100 and 1123 are effective in fire-tube and water-tube boilers alike. The polymer package in each will work to keep boiler surfaces clean at operating pressures of 300 psi and below. Our boiler polymers are also effective for boilers of any horsepower.
Q: How will I know if Formula 1100 or 1123 is working effectively?
A: Annual inspections are vital to effective boiler operation. Boilers that are treated with Formulas 1100 and 1123, and protected from significant feedwater upsets, will show noticeable improvements in cleanliness with excellently passivated surfaces at time of inspection.
Q: Beyond the product, what is the advantage of adding Garratt-Callahan to your boiler room team?
A: Your designated Garratt-Callahan representative will visit your facility to verify that Formula 1100 or 1123 is at an effective residual in your industrial boilers. The highly accurate traceability provides assurance that the product is present. A professional report of your boiler treatment program will be delivered after each service visit, verifying that you are on track for a clean boiler.
The G-C Advantage
The G-C Advantage program takes into account the monitoring and testing to reduce the maintenance cost and downtime while preventing any risk of damage.
- Eliminate Non-Mandatory Cleanings
- Testing & Treating Feedwater
- Reduce the Risk of Handling Hazardous Chemicals
- Ease of Service for Confined Space Entries
- Staying Informed With G-C’s Preventative Health Checks
Garratt-Callahan provides the expertise, training, and all the chemicals needed to get your boilers serviced with treated water and operating at maximum efficiency.
Contact us to learn more about the Garratt-Callahan Formula 1100 and 1123, and how your industrial boiler maintenance fits into the G-C Advantage program.
Connect With Industrial Water Treatment Expert
Garratt-Callahan started with servicing the boilers that powered steam-locomotives of the Industrial Revolution. Our expertise in industrial water treatment service continues today for all types of industries and facilities. Our water treatment expertise — demonstrated through on-site consulting, chemical applications, equipment maintenance, and customer service — are more than just 100+ years old. Our client relationships are built on fairness, honesty, and integrity. By thoroughly understanding your needs and challenges, we can roll up our sleeves to find sustainable solutions that work.
"*" indicates required fields