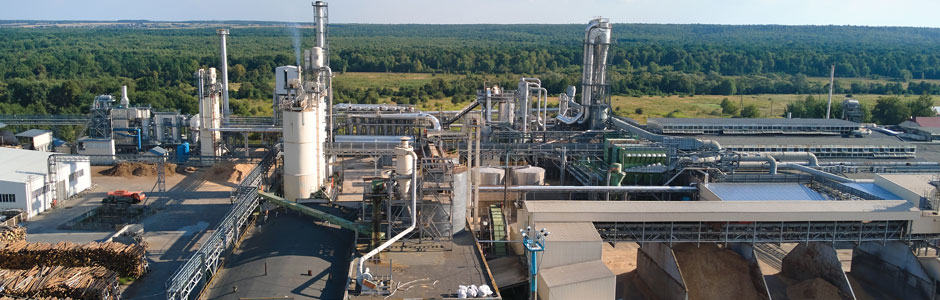
I. Challenges
A lumber company in East Texas experienced high corrosion in their steam kilns resulting in expensive replace/rebuild costs. They were going through the following issues:
- High-pressure cycles as low as 3, causing them to blow down 13,343 gallons/day
- Boilers consumed 3,100 gallons of water and 325lbs of salt per day
- Approximately 16,421 gallons of wastewater had to be disposed of by boiling off water and trucking away solids
II. Approach
Garratt-Callahan’s team analyzed the site’s source water and kiln chemistry. They found that the company’s boiler water carry-over and high levels of chloride problem were due to the softener/dealkalizer system.
Based on the team’s calculation, using reverse osmosis permeate as the boiler feed would increase the boiler cycles from 3 to 30. Therefore, the team replaced the softeners/dealkalizers with an RO unit to pretreat boiler water.
Pretreatment to the RO included a greensand filter to remove iron followed by 5 and 1-micron cartridge filters to remove suspended solids. As a result, they were able to:
- Eliminate high levels of chloride and water carry-over in the kilns
- Remove the need for softeners and eliminated wastewater and solids from the regeneration
III. Results
The installation of the RO system for boiler pretreatment avoided kiln replacement/rebuild that could cost $250,00 per event. In addition, the team’s resources and corrective actions resulted in the following:
- Softener regeneration and other associated costs were eliminated.
- Reduction of water usage by 4,295 gallons per day
- Decreased sludge treatment and disposal costs by 25%
- Nearly $60,000 in projected annual savings with a payback time of just 1 year
The lumber company’s site manager who once believed RO would cause increased water waste provided this feedback, “I am very impressed with the RO unit’s performance and cost savings it has yielded to our company.”
"*" indicates required fields